Dredge No.5 - The Lonely Giant of Tanjung Tualang
- Ammar, R. & Izzaty, N.
- Jun 20, 2021
- 9 min read
Updated: Jun 2, 2023

Accompanying music: Welcome to the Machine ~ Pink Floyd
Tin mining has always been an integral part of Perak's development, bringing the state and its inhabitants riches throughout the 1800s and 1900s. Among the remnants of this industrious past, lies the 'TT5', a towering metal machine, floating peacefully in one of the hundreds of mining ponds in Tanjung Tualang. Once part of a large dredging fleet in the minefields of Kinta Valley, this lone giant is currently the only one left of its kind, a rare gem of Perak's prosperous tin-mining history.

3-meter-deep pontoons supporting TT5's enormous weight.
Formally named 'Dredge No.5' (now known as Tanjung Tualang Dredge No. 5), TT5 is located in Batu 6 Jalan Tanjung Tualang, about 30 kilometers from Ipoh. The machine is anchored in an enclosed pond 200 meters from the main street, facing a huge plain dotted with hundreds of ex-mining lakes. These mining fields stretch far eastwards, towards the karst hills of Gunung Tempurung and Hutan Lipur Sungai Salu.
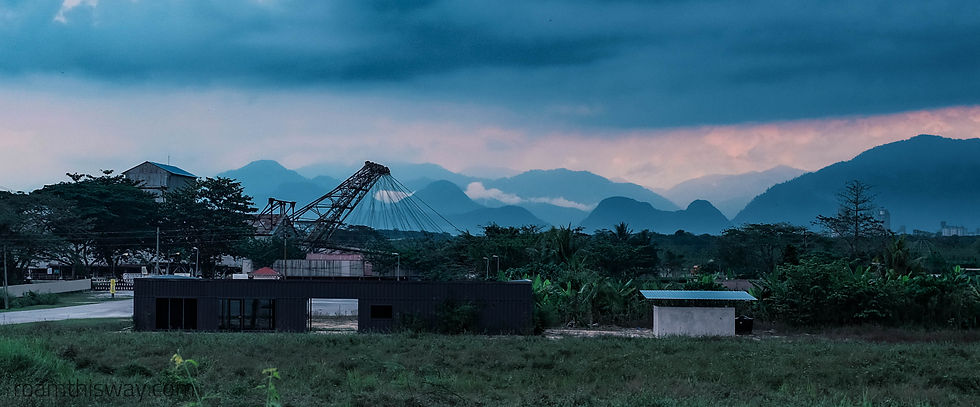
A stunning backdrop of Gunung Tempurung and other Kinta Valley limestone hills.

Map of TT5's location from Ipoh city center.
Seen from afar, TT5's silhouette could easily be mistaken for a factory building and a yard of large cranes. Spanning 75 meters in length, 19.5 meters in width, and 5 storeys high, its monstrous figure dwarfs everything around it. Huge rusty metal buckets and beams hang onto its front and back sides, while rows of pontoons underneath steadily keep the 4,500-tonne machine afloat.
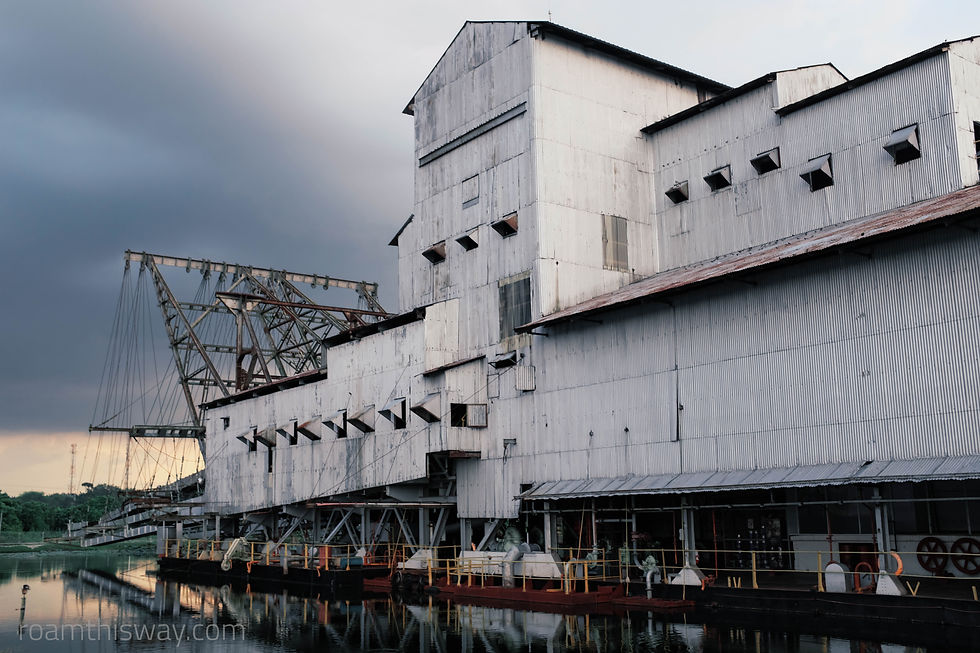
Tanjung Tualang Dredge No.5 (starboard side, facing towards the stern).
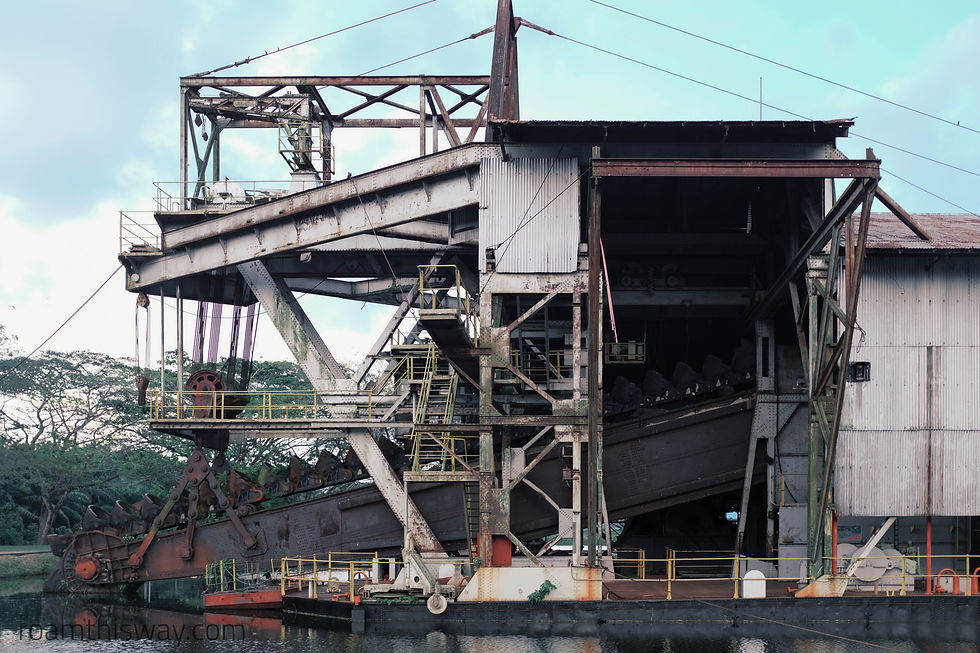
Dredge bow gantry with bucket chain, hoist gears, giant pulleys and bow crane. Guy-ropes used extensively to provide additional support.
Invasion of the Metal Monsters
Between the middle and late 1800s, the tin mining industry in Malaya was mainly dominated by Chinese miners, giving rise to many mining towns in Lembah Kinta (including the nearby town of Papan). Due to equipment and labor issues, western companies struggled to compete with these miners, resulting in only a handful of them operating in the Federated Malay States (FMS) at the time.
The fact that the mines in the states being mostly of the shallow alluvial type also proved problematic, as these companies were more accustomed to working on lode mines (much deeper ore veins and required different methods to extract). To their fortune, this monopoly started to change with the introduction of dredges.

5-storey-high structure with corrugated metal sheet facade (port side view). The top section houses the main drive motor assembly and upper tumbler for the bucket chain system.

Front (bow) side of the dredge. The enclosure on the upper floor is the pilot house.
Mining methods used by locals included traditional dulang washing (panning), using simple tools such as changkol, lampan, lanchut and water wheels, followed by the more recent hydraulic approach of applying gravel pumps and palongs. With these local techniques in practice, the arrival of dredges was indeed a paradigm shift.
Originally designed in the 1880s to increase gold extraction in New Zealand mines, bucket dredges were further improved to be operated in Australia, the United States, and Canada. Once reaching Perak, the technology underwent some further modifications after failed attempts in 1891 and 1912. The first successful use of a bucket dredge was finally achieved in 1913, introduced by Malayan Tin Dredging Ltd (not to be confused with Southern Malayan Tin Dredging Ltd, its sister company) to work on minefields near Batu Gajah.
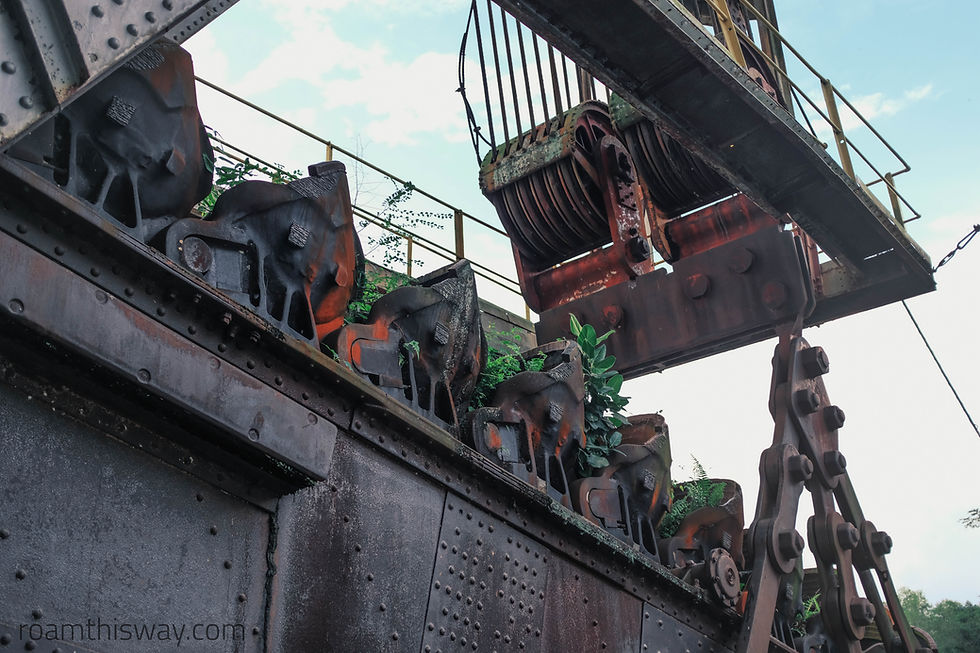
A closer look at the bucket band, 'decorated' by shrubs and moss.
Dredges had the major advantage of being able to operate continuously and autonomously, equating the capacity of a small 12-bucket dredge to an army of 2,000 coolies. In addition to this, the huge initial cost of dredges became an entry barrier for smaller-scale miners, while much larger companies had an upper hand in securing investments. Naturally, this gave the foreign companies a massive economical and competitive advantage over the Chinese miners.
Despite the outbreak of the first World War and international shipping restrictions, the use of these machines grew steadily, with well more than 100 dredges reported to be in operation throughout Malaya by 1929. In a few year's time, western companies grew to producing more than two-thirds of tin ore in the country (both through open-cast and dredge mining methods), far surpassing their local competitors.
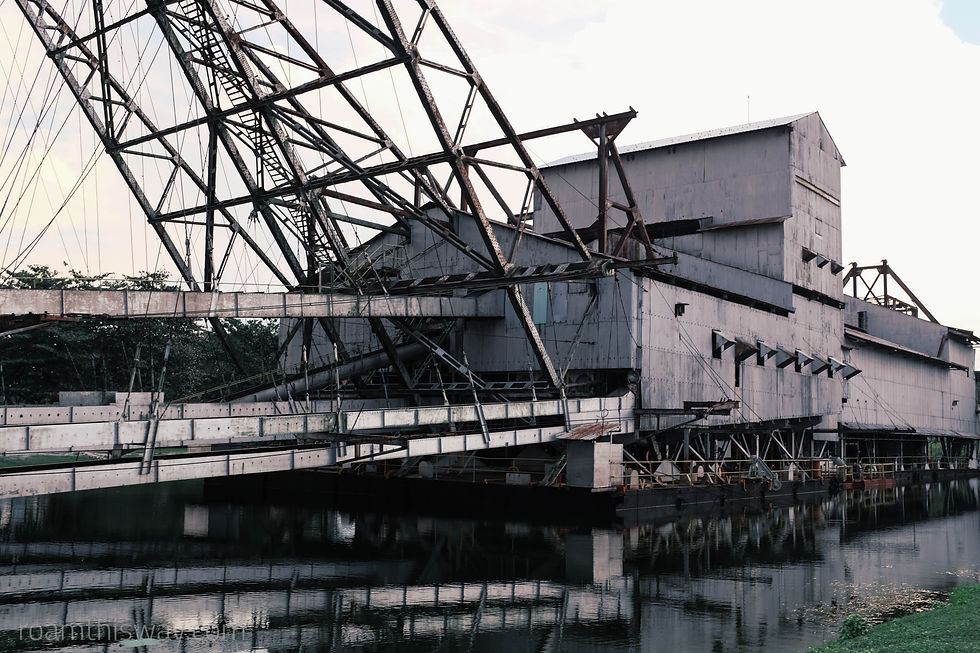
Dredging machines were once famous for working on the Canadian Yukon Valley goldfields.

Hatch for the save-all sluice chamber, where small amounts of tin grains were collected and 'saved' from being wasted.

Water pump piping for breaking down and washing of ore-bearing earth.
Floating Factory
Each dredge is essentially a complete mine, self-sufficient in conducting excavation and ore dressing without any other external machinery. The bucket line dredge (or ladder-bucket dredge), a type of dredge most commonly used in alluvial tin ore mining, uses a bucket chain system, scooping and bringing karang (ore-bearing earth) on board, followed by screening, separation, shaking, and washing of tin ore from other materials using a system of monitors (pressure jets), rotating trommel screens, sluice tables, and multiple sets of jigs.
The trapped tin ore fragments (in the form of raw Cassiterite, a tin oxide mineral) are then collected and channeled into storage bins to be transported out, while amang (tin tailing; fine mineral waste) and overburden (coarse waste and rocks) are separated and disposed at the stern through chutes or stackers.

Stern gantry boom providing suspension to chutes. Barb wires (bottom right) installed to stop scavengers from entering the dredge.
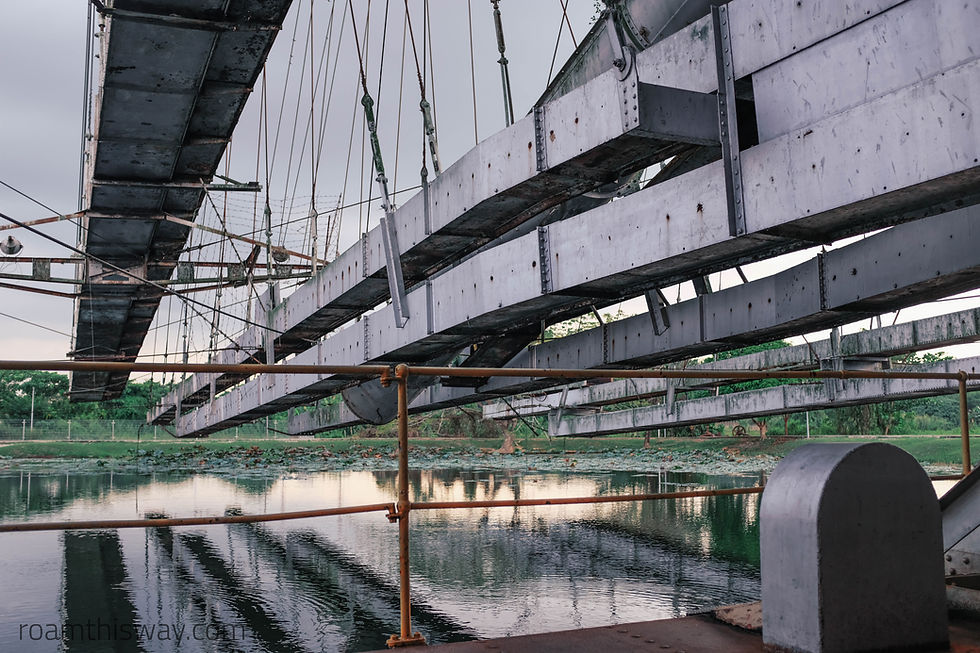
Waste chutes at the dredge stern, used to deposit non-valuable mining by-products, sand, oversized soil and rocks onto the pond banks after processing.
The TT5 is one such dredge, and among the larger ones used in Perak too (it is, however, considered to be 'medium-sized' compared to its other Tanjung Tualang companions). The dredge was fabricated in England in 1938 by F.W. Payne & Son, with its 2,247 hp engine and intake water pumps supplied by Allen West Co. Ltd.
Equipped with a massive ladder fitted with 115 close-connected buckets, TT5 could reach excavation depths of more than 30 meters and had a capacity of handling 358,000 cubic meters of material per month. Its dredging buckets, weighing around 2 tonnes with a capacity of 0.5 cubic meters each, were made out of hardened manganese steel alloy, allowing increased impact and abrasion resistance. The attached lips (which seemed to be welded instead of rivetted onto the buckets) were possibly made of the same alloy.
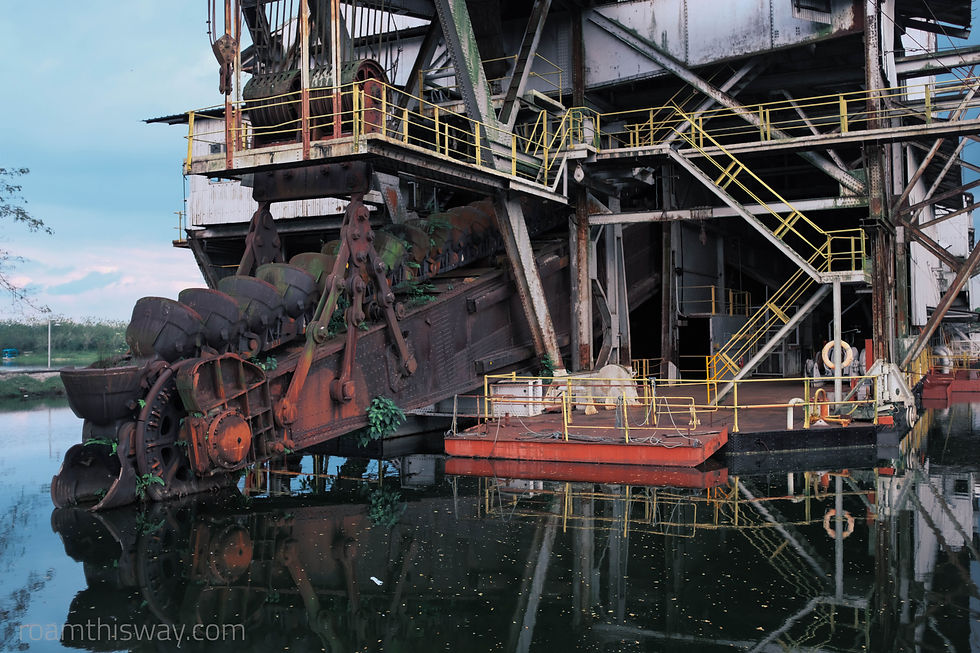
Raised bucket line, with lower tumbler visible at the end of the digging ladder.

TT5's bucket line had 2-speed settings; 22 & 26 buckets/min.
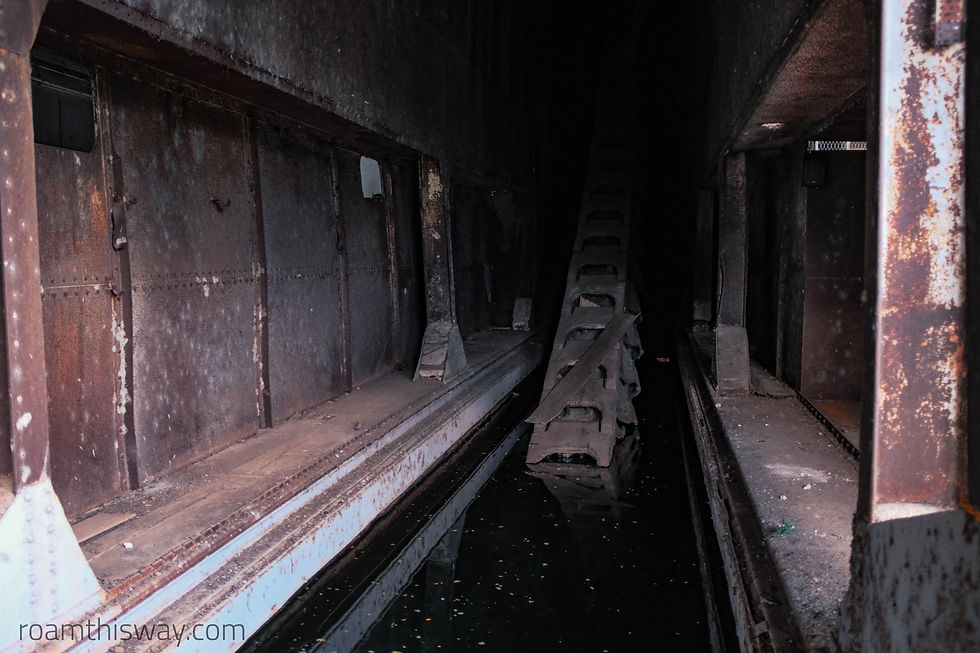
Bottom part of the bucket line, additionally driven by an idler sprocket at the far back.
TT5's manpower was separated into three shifts, with each one having a head-count between 12 to 30 workers on board. Staff facilities in the dredge include an eating area, resting space, lockers, and restrooms (which directly discharged into the pond below). Compared to the small manpower required, TT5 was able to extract an excellent output of around 30 drums per day.
After completing dressing on board, the tin ore concentrate was poured into waiting drums on the primary deck. Once filled, the drums were hooked onto railings and moved towards waiting sampans outside. The minerals would then undergo final processing at the Straits Trading Butter-Worth Smelter, a smelting plant located in Penang.

Outlets for channeling processed tin ore (left), and heavy drums (right).

An old sampan, possibly used for transporting tin-containing bins out of the dredge.
The TT5 also had a peculiar way of moving about. Instead of using propellers like on most watercraft, dredges maneuver and rotate through a 'wire positioning system', using a network of winches, anchors, and mooring cable lines attached to both the dredge and surrounding land. This system is controlled by adjusting the winches directly from the pilot house. Additionally, dredges were also able to move from one spot to another via simply digging forwards and simultaneously depositing back the soil at the stern, thus 'carrying' the surrounding pond together with the machine.

Stairs towards the pilot house and winch room above.
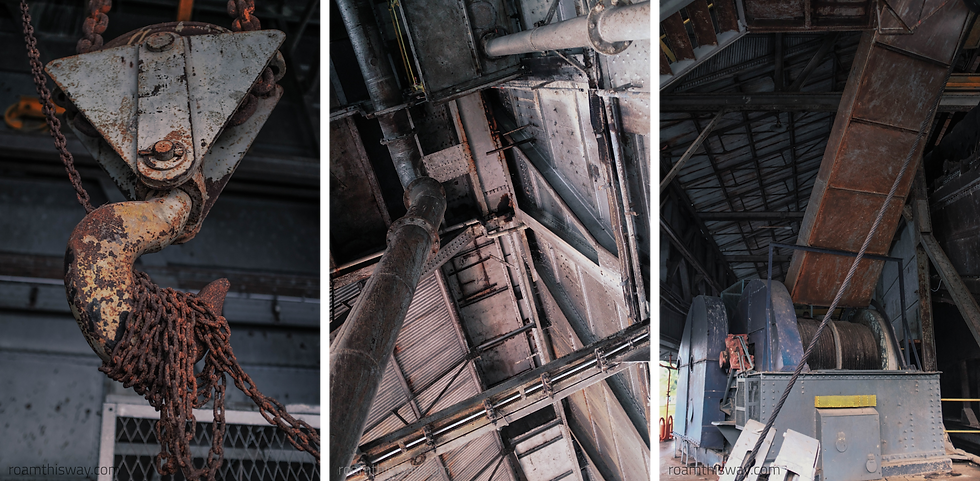
(From left to right) Chain block, pipes from suction pump, ladder hoist winch drums.
Tanjung Tualang & TT5
As indicated by its name, TT5 was used mainly in Tanjung Tualang, about 10 kilometers down the road from its current location. This village, named after a type of tree (or from a personality named 'Toh Alang', depending on who you ask), was a swampy area in the mid-1800s, mostly dotted with rubber estates, small-time fishermen, and virgin forests.
The first tin rush in the mid-1800s saw some mines being opened here, operated by both Malays and Chinese miners. Sultan Ismail, who owned the famous Papan mines around 20 kilometers away, also had several mines in Tanjung Tualang during this period. Despite the initial growth in activity and railway connection in the nearby Kota Bahru, the fields became less economical, and interest soon fizzled out.

Railway links in Perak in the early 1900s. Kota Bahru station is shown on the lower right side.
(Ref: Adapted from www.Malayarailway.com map)
The 1920s witnessed an explosion of mining activity in Tanjung Tualang. Through the application of deep boring prospecting, hydraulic extraction, and dredging technologies, the surrounding area of this small village was transformed into the largest tin mining operation in the whole Kinta Valley. Forests were stripped, while rubber estate lands, fishing areas, and even the whole village itself were shifted to make way for surface mines, labor housing, and of course, dredges.
Local Chinese mines (such as Toh Allang Chinese Tin Company Ltd and Kwong Yik Tin Mine) found themselves surrounded by an influx of internationally funded companies, among them including; Tanjung Tin Dredging, Malayan Tin Dredging, Kramat Tin Dredging, Southern Tronoh Tin Dredging Ltd. and Lower Perak Tin Dredging Ltd. and Southern Malayan Tin Dredging Ltd (SMTD). Apart from commanding large capital and successful application of dredges, many of these foreign companies were also connected with each other through interlocking directorship and formation of conglomerates, further strengthening their hold of the local mining industry. The capacity of these entities was so large that ore production output had to be restricted in 1929 to avoid a worldwide oversupply of tin.

Gantry crane (midground) and eating/rest area for staff (background).
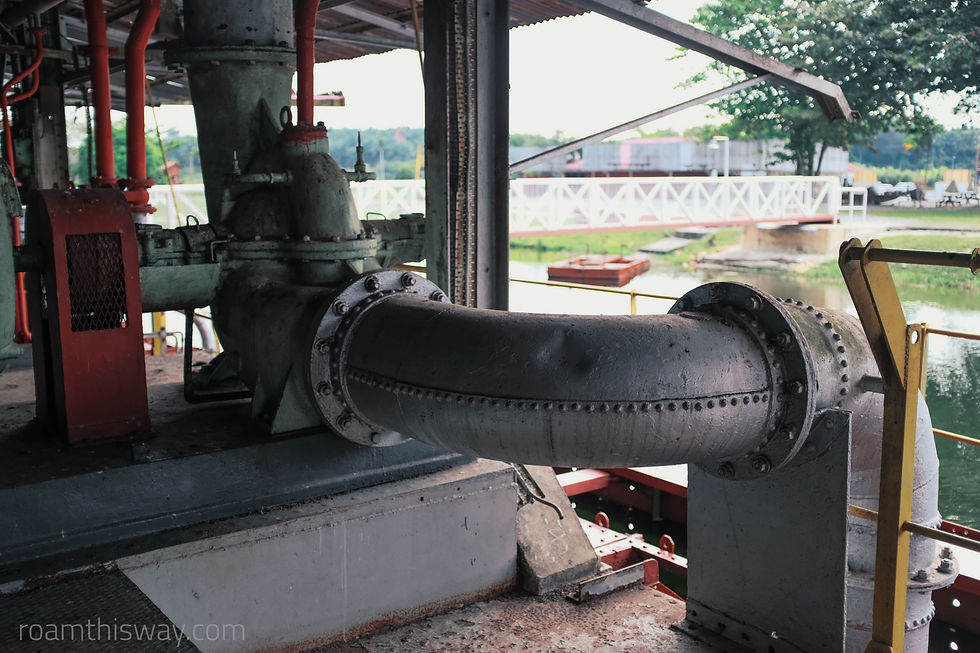
Centrifugal pump pipes and valves on the primary deck level. TT5's footbridge can be seen in the background.
SMTD was the first owner of the TT5. As indicated by its prefix "Dredge No. 5", TT5 was one of five dredges operated by the company in Lembah Kinta. These dredges worked on 3,661 hectares of land eastwards of Tanjung Tualang and Batu Gajah. Beginning its operation in 1938, TT5 started with minefields in Teja (near Gopeng) and slowly made its way to Tanjung Tualang.
Throughout the mid-1900s, Tanjung Tualang went through the troubling times of World War II and the subsequent Malayan Emergency. Between 1948 and 1950, its community experienced attacks, ambushes, abductions, infrastructure sabotage, and even murders by communists guerillas. Regardless, TT5 continued to remain operational in the many years ahead, even going through a major upgrade of replacing its coal-fired steam engine with an electric-powered one in 1963.

Access hatch to hull space below deck. The pontoon section underneath is said to have multiple escape routes to be used by workers during emergencies.
Some time after the Malayan Independence, SMTD was incorporated as Southern Malayan Tin Dredging (M) Berhad, an entity owned by Malaysian Mining Corporation Bhd (MMC). Considered to be the world's largest integrated tin producer, MMC is the corporate successor to Malayan Tin Dredging Ltd.
The early 1980s saw the tin industry taking a sharp fall. Widespread recession, overproduction, and rising popularity of aluminium as a substitute material were some of the factors that resulted in the global reduction of tin prices. Influenced by such economic pressures, MMC decided to cease all tin mining operations in Malaysia, including its operations in Tanjung Tualang. As such, TT5 was finally retired in 1982, just a few years before the Tin Market Crash of 1985. Unlike its other companions, TT5 was not sold off nor dismantled for scraps. The dredge was instead donated to the Perak State Government in 1997 for the purpose of education on Malayan tin mining history. Management of the dredge was subsequently given to Batu Gajah District Council and later Osborne and Chappel Sdn Bhd.

Sound produced by TT5 could be heard around 2-3 kilometers away. Such noisy work environment required the use of meeting bells to get workers' attention.
After quite a number of years, the dredge fell into disrepair, mainly due to lack of funding. A 'Save the Dredge' campaign was initiated after the discovery of major leaking and tilting of the whole hull. Fearing the loss of such a valuable piece of history, the state government oversaw both its management and restoration in 2015. MB Incorporated (MB Inc) was given the task to take the reigns, with public funds amounting to RM8.5 million injected to finance repair works.
As of 2021, TT5 is one of the two last tin dredges in Malaysia that still retains its historical roots from the tin-producing golden age (the other one being the heavily dilapidated Sri Banting Dredge in Selangor).

Close-up view of winch drum instrument.
TT5 presently stands as a unique exhibit of tin mining history in Perak and Malaya at large. Visitors could explore the inner workings of this tin monster whilst surrounded by a vast post-mining landscape; dredged ponds, embankments, tailing dumps, and mullock mounds, as far as the eye could see.
In spite of its lasting impact on Perak's natural environment, the tin mining industry has grown to become a part of Perak's modern identity, inseparable from its history books and its people. While heated debates on Perak's land exploitation continue to this day, the preservation of TT5 ensures that one of the historical gateways into this past is kept open.
***

View of a man-made lake in Tanjung Tualang.
References/Further reading:
Batu Gajah Municipality Website: www.mdbg.com.my
Lembah Kinta History: Kinta Valley: Pioneering Malaysia's Modern Development (Khoo Salma Nasution & Abdur-Razzaq Lubis, 2005) - Perak Academy
TT5 operation details: 4,500-ton tin monster resurrected as tourist attraction (Chan Li Leen, 23/12/2017) - The Star Online
TT5 before 2015: 'Harta' yang ditinggalkan (Special Report, 23/3/2013) - Utusan Malaysia
TT5 after repairs: Kapal Korek Tanjung Tualang bukti kejayaan Perak (Hidayah Mohammad, 7/1/2018) - Berita Harian
Dredge master accounts: Warisan kapal korek terakhir (Shaarani Ismail, 13/5/2016) - Berita Harian Online
Dredge repair campaign: Save the Dredge (2011) - Osborne and Chappel Sdn Bhd
Development of dredging technology: From Klondike (Yukon) to Kampar (Malaya): The transfer of dredging technology by Yukon Gold Company (Shakila Yacob, 2013) - Vidyasagar University Journal of History
Communist activity in Tanjung Tualang: Pergerakan Komunis di Negeri Perak, 1920-an Hingga 1960 (Ho Hui Ling, 2012) - Malaysia Dari Segi Sejarah, Persatuan Sejarah Malaysia
Tin Mining in Malaya: Tin Mining in Malaysia- Is There any Revival? (Yap Keam Min, 2007) - Jurutera
Southern Malayan Tin Dredging Ltd details: www.thediggings.com
MMC History: www.mmc.com.my
great photos and article, and matching with this song "Welcome to the machine" (especially the intro of the music).